Advertisement
A Boeing whistleblower speaks out
Resume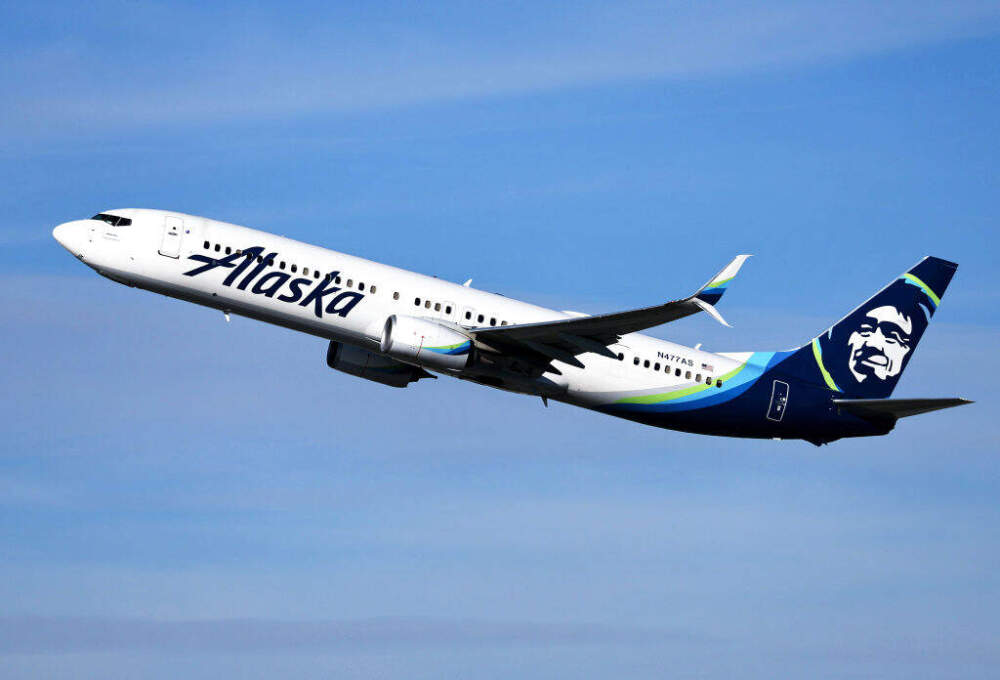
Ed Pierson is an aviation manager who used to work on Boeing's 737 Max production line.
When a door panel blew off an Alaska Airlines flight, Pierson wasn't surprised.
Today, On Point: A Boeing whistleblower speaks out.
Guest
Ed Pierson, director of the Foundation for Aviation Safety. Former senior manager at Boeing's 737 Factory in Renton, Washington.
Transcript
Part I
MEGHNA CHAKRABARTI: Last month, Alaska Airlines Flight 1282 took off from Portland, Oregon toward Ontario International Airport in Southern California. The plane ascended through a routine first six minutes. The Boeing 737 MAX 9 aircraft was about halfway to cruising altitude when suddenly a panel plugging an unused door behind the left wing, blew out. The plane immediately depressurized.
Now this terrible event could have turned into a catastrophe, but thankfully did not. Two seats next to the hole were unoccupied that day, and the crew kept their heads and safely landed the plane back at Portland International Airport. The incident was not fatal, but in a lawsuit filed by several passengers.
They say the incident left them traumatized and physically injured. Now you've heard of the 737 MAX before, of course, in 2018 and 2019. Two 737 MAX 8's, Ethiopian, Airlines, Flight 302 and Lion Air Flight 610 crashed due to control system failures on the aircraft that prompted a temporary worldwide grounding of the entire 737 MAX fleet, both 8 and 9's.
The FAA lifted that grounding November of 2020. It was 20 months long. A grounding that was the longest ever for a U.S. airliner. Now there's scrutiny back on the 737 MAX again. With Alaska Air 1282, we have a mechanical failure of a 737 MAX 9. Ed Pierson joins us today.
He's not just an aviation safety expert. He has truly unique insight into these specific aircraft. Ed, welcome.
ED PIERSON: Welcome. Thank you very much for having me.
CHAKRABARTI: I should say, Ed, that you are currently, and for the past several years, you have been director and are director, executive director of the Foundation for Aviation Safety.
But prior to that, where did you work?
PIERSON: Prior to that, I worked at the Boeing company inside the 737 factory.
CHAKRABARTI: The 737 factory that builds the 737 MAX planes.
PIERSON: Yes, that's correct.
CHAKRABARTI: And that's in Renton, Washington?
PIERSON: Yes.
CHAKRABARTI: How long did you work there?
PIERSON: I worked at the factory for three years.
CHAKRABARTI: And what did you do?
PIERSON: I was a senior manager in the production system support organization, and we supported the building of the airplane.
CHAKRABARTI: So tell me in more detail what that means. What was your day-to-day job?
PIERSON: I had two groups that I was responsible for. One was the industrial engineering group, which took the responsibility for all the planning of the build and all the details associated with how everything came together.
And then there was another group that was called ship side, and that group was really more of a response organization. Whenever there was an issue with the problem on the airplane, they would come over and our team would assist that individual to get the whatever they needed, parts, engineering, drawings, quality assistance, what have you.
CHAKRABARTI: Is it fair to say, Ed, that these aircraft, the 737 MAX pretty well?
PIERSON: Yes.
CHAKRABARTI: How well would you say you know them?
PIERSON: I think I know them pretty well, we're still learning some things and things we're learning, not necessarily good.
CHAKRABARTI: Okay. Why did you leave in 2018?
PIERSON: I wasn't planning on it. I was actually hoping to spend another five or seven more years at the company and I started seeing a serious decline in everything. Every facet of the company inside the factory was a mess. We were rushing planes out the door. Employees were reporting all kinds of issues.
My team and other teams were expressing frustration. There was people working ridiculous amounts of overtime and all our performance metrics in the factory were going in the wrong direction. And it was just a uncomfortable place to be. I didn't support the leadership, the way they were treating employees, and I just didn't think it was a healthy place to work, and I knew I needed to get out of there, so I decided to retire early.
CHAKRABARTI: Did you feel like you needed to get out because you were concerned that Boeing was sending unsafe planes out the door?
PIERSON: Yes. That was a big part of it.
CHAKRABARTI: So when you say that they were rushing to get planes out the door. To me, it's hard to understand what that means given the size and complexity of these aircraft.
And ostensibly, the very fine scrutiny that they're under, both within Boeing, from the manufacturing process, and then also, of course, from regulators and customers. So can you tell me more detail, what it means to rush a plane? 737 out the door.
PIERSON: Sure. You have to understand that this complex is gigantic.
It has thousands of employees working in it. There's three assembly lines and each assembly lines has about nine or 10, what we call flow days. So the fuselage would get trained in from Wichita, Kansas, that would get lifted into flow day one, and then the build process would begin. And that's where they started to install all the infrastructure of the airplane, like the plumbing and the electrical and the insulation.
And as the plane went down the line, then in flow day four, the wings would be joined and then it continued down the line. And so every day, all three lines, these airplanes are moving. Every night they're getting moved to the next position. So you have a couple thousand employees who are building the plane in three shifts, basically seven days a week.
And each person, that manufacturing employee would have a certain number of jobs to perform. So you might have four jobs, I might have three jobs depending on the duration. And every day you were expected to perform those jobs. And when you have the proper training and the proper supervision and quality control, and you have all your parts and you're well rested, people do amazing work.
That's what the company's done for many years. But what we were seeing was a shortage of parts that were coming in. First it started with their engines coming late. Pretty darn important part for an airplane. And that started a cascading effect. Now we started seeing other suppliers sending their parts into us late, and unfortunately the plane keeps getting moved down the line.
It's called at a sequence work. So let's say you work on flow day three and you go to install your parts and they're not there that day, so you can't do your work. The person following you may not be able to do their work because you didn't do your work. And it's a very potentially dangerous situation.
And that's what I was seeing. And so employees were very tired. There was lots of reports, like I said, on defects and mistakes being made, process breakdowns all over the place.
CHAKRABARTI: Okay. So we're going to come back to the things that you saw on the line a little later in the show, Ed, but you've already said so much that it really undergirds.
I'd say the reason why we're privileged to have you on the show today, because after you left Boeing, as I said, you became executive director of the Foundation for Aviation Safety. Now, regarding that, Alaska Air 1282 flight. I actually understand that even before this year, that in fact, last year, spring of last year, you sent a letter to the CEO of Alaska Airlines.
What prompted you to do that and what was in the letter?
PIERSON: If I could just, let me just go back. Because I want to make sure that people understand. After I retired from the company, I became a safety advocate, and it was our foundation that was created very recently. It's only about six months old.
But as far as what wrote, what caused me to write the letter to the CEO myself and another gentleman named Joe Jacobsen, who's a former FAA aerospace safety engineer. We've been closely monitoring the airplane's performance. After it was recertified and we started seeing all kinds of evidence of production, quality defects, brand new planes coming out with systems failures that should never happen, especially on new planes.
And this included everything from engines to anti-icing to flight management, computers, autopilot. It was just a very diverse range of issues, and it was concerning. So it just so happened that Alaska Airlines had submitted over 1,200 reports on 53 new airplanes in a year, two-year span of time. And so we were looking at this information and I wrote a letter in April to the CEO pointing out the obvious production quality defects that were occurring on his planes.
And he just never responded. He ignored it. Then we, our foundation, wrote a report in September, and we detailed out these issues. And Alaska Airlines media, people called us, left a message. I called them back, left a message. They never returned our call after that.
CHAKRABARTI: Okay. So these 1,200 reports that you said Alaska Airlines had filed, can you clarify for me, where were they filing these reports to and how did you get the information?
PIERSON: Okay. So there's a title XIV Law that requires U.S. aircraft certificate holders to submit to the FAA reports of aircraft system malfunctions, and that is called the FAA Service Difficulty Reporting System. It's a very un-user-friendly database that the FAA maintains. And it's actually quite difficult to find sometimes, if you're not, don't know where to look.
And it's even more difficult to query because you have to know the nomenclature of the airplane. So we were able to because we have experience in this, we were able to extract the data out of that. And just kept doing analysis and we've been talking about it. We actually created a podcast to help get the word out about it.
And as we were looking at all this data it was very concerning because, again, new airplanes should not be having these kinds of problems.
CHAKRABARTI: And this database is, it's public. It's supposed to be public.
PIERSON: It is public.
CHAKRABARTI: Okay.
PIERSON: It's called the FAA Service Difficulty Reporting System. But I'll just tell you it's even for people that are aviation types. It's a pain to query. Go ahead.
CHAKRABARTI: Sorry, I didn't mean to interrupt there, but so again, the details really matter here. Ed you're an engineer.
PIERSON: Yeah.
CHAKRABARTI: So you understand that the details really matter. 1,200 reports from Alaska. Were you looking for specifically 737 MAX reports or just kind of all reports on new aircraft coming out of Boeing?
PIERSON: No, we were just looking at 737-8 and 737-9 MAX airplanes.
CHAKRABARTI: So 1,200 reports just from Alaska on those two model of aircraft.
PIERSON: They just have the 737-9.
CHAKRABARTI: Okay.
PIERSON: And what people have to understand is Alaska's headquarters, is the Alaska is probably the closest.
It is the closest airline in the world to the 737 program. It's right down the road, 20 minutes down 405. And if that plane is having problems with the, you know, if that airplane is having problems there, we're wondering what's happening overseas.
CHAKRABARTI: Would you fly a 737 MAX today?
PIERSON: No. No way. I actually was put on one accidentally and I had to walk off the plane.
Part II
CHAKRABARTI: I should note that we definitely reached out to Boeing for comment, a statement for them to provide someone to us to join us live today. They were unable to do that. They did point us to recent comments that Boeing's CEO made in a quarterly earnings call regarding the Alaska Airlines flight failure. We'll hear a little bit more from those earning call moments in just a few minutes. But first of all, let's just hear the voice of a passenger who was on Alaska Air 1282.
This is Elizabeth Le. She spoke to [a] CBS affiliate ... about what happened.
ELIZABETH LE: All of a sudden, I heard like a big bang, and I didn't know exactly what was going on, but I look up and the oxygen masks were hanging from the ceiling. And then I look to my left and there's this huge chunk, part of the airplane just like missing. And the wind is just extremely loud. There's wind blowing everywhere.
CHAKRABARTI: So that's a passenger Elizabeth Le. Now Boeing CEO David Calhoun met with lawmakers on January 24th, as Boeing grounded all of its 737 MAX 9 planes. And on his way to his meeting, he assured the media about his confidence in the company's planes.
DAVID CALHOUN: We fly safe planes. We don't put airplanes in the air that we don't have 100% confidence in.
CHAKRABARTI: It's Boeing CEO David Calhoun on January 24th, and here is Calhoun again after the blowout of Alaska Air 1282, speaking to Boeing employees about the issue.
CALHOUN: We are going to approach it with 100% in complete transparency every step of the way.
We're going to work with the NTSB, who is investigating the accident itself, to find out what the main cause is. The FAA who has to now deal with the airline customers who want their airplanes back in service safely, and to make sure all the procedures are put in place, inspections, all the readiness actions that are required to ensure every next door playing the wolves into the sky is in fact safe and that this event can never happen again.
CHAKRABARTI: That's Boeing CEO David Calhoun. Now, Ed, what I'd like to do for the next several minutes here is dig into the NTSB's preliminary report on Alaska 1282 here. Because I read through the whole thing.
It's definitely written in aviation-ease, but I'd love to have you decipher for us a little bit of what the NTSB is saying is a possible cause for this failure. This is a fairly recent report, but again, I emphasize it's a preliminary one. Okay. So first and foremost, they say that this particular aircraft was delivered from Boeing to Alaska Air on October 31, 2023.
So as you were saying earlier, it's a new aircraft. It had that failure, what, three months later?
PIERSON: Exactly.
CHAKRABARTI: Okay. So normally, in the first three months of an aircraft's life span, they're not perfect machines, but what would be normal anomalies for an airplane that you might expect?
PIERSON: It's a brand-new plane. You wouldn't expect any anomalies. You expect that plane to be perfect.
CHAKRABARTI: Okay. Okay. I was, I just want to check, because I didn't, I don't really, I'm not an expert in what the tolerances are for errors in anomalies in aviation. So they're pretty tight, is what you're saying.
PIERSON: And obviously some of these airlines have been flying very old planes, so they're used to dealing with some issues. But if you had a brand-new car, you wouldn't expect it to have problems. Okay. And I would like to make, if I could at some point, I would like to respond to the comments that the CEOs made because I think it's very important to address them directly.
So I hope we can talk about that actually.
CHAKRABARTI: Why don't talk about that. Yeah, no, why don't you go ahead and do that now, because the NTSB report is sitting here in front of me and we can get back to it.
PIERSON: Okay, first of all, unfortunately, I think when CEO Calhoun's speaking about transparency and doing everything right.
I gotta tell you, I feel like it's a hog wash because we've heard this before. We heard this before the first plane crash occurred, that the plane was perfectly safe in a wonderful plane. We heard it after the first crash. We heard it again after the second crash. We heard it after certification.
CHAKRABARTI: This is 2018. 2019, right?
PIERSON: Yeah.
CHAKRABARTI: Okay. Go ahead.
PIERSON: 2018. 2019. We heard it after it went through a grueling 20-month recertification, we heard it again after the plane was grounded for an electrical issue shortly after being recertified. And now we've heard it again after the Alaska accident. And so really, we've heard this over and over again.
And those words really sound very shallow to me. And as far as transparency and speaking with employees and speaking with lawmakers, one of the issues that we've been pointing out is the CEO and the C-suite and the board of directors need to get out of their chairs and go down and spend time on the factory floors with these employees.
So when they work with these, when they get on the floor with these employees, they're going to learn more in a day than they would in 50 PowerPoint briefings. And that's really important because if they don't see it, if they don't understand those challenges, then it's easy for them to get out of touch.
And unfortunately, that's what's happened and it's unfortunately not just the 737 program. And as far as transparency goes, and I look forward to talking to you about the NTSB report, but what people don't know, they've heard the story about the first two crashes. Everybody in the world has heard about the MCAS software and the lack of pilot training and the rush design.
All of that is true. But those two airplanes, both of those airplanes also had serious manufacturing defects, electrical defects in those airplanes. And I've written reports on it. We've been pushing this information out. And it's very frustrating because that was never investigated. In fact, I know this is shocking to people, but I have an email here from the managing director of the NTSB to myself and a mother who lost their 24-year-old daughter.
And the NTSB after we asked them, after we confronted them, they acknowledged that they never went in and investigated the Boeing manufacturing in the factory after a two-month-old and a four-month-old plane crash. So meanwhile, they're telling the world that they're going to fully cooperate and they're assisting the international investigators.
And it didn't happen.
CHAKRABARTI: Wait. Ed, I'm sorry. I want to be clear. Who didn't go back into the Boeing factory to investigate manufacturing?
PIERSON: So when a accident happens overseas, the country where the accident occurs automatically assumes what's called the investigator in charge responsibility under International Standard Annex 13, which is a international civil aviation organization standard, and then all the other parties are in a support role. They're in the position where they provide information. So in the United States, the NTSB was in what's called an accredited representative role, where their job was to basically be the lead for the U.S.
And their job was to coordinate with the manufacturer Boeing and the regulator, FAA. And the NTSB, all the parties to an investigation are responsible for sharing relevant information. That didn't happen, and not only did it not happen, even though I had written extensively to the NTSB after the crashes. I had written to, I had talked to the general counsel of the Boeing company, I had written to the board of directors.
All that happened after the first crash, the NTSB, even after all that, did not investigate Boeing manufacturing. And again, it was a two-month-old, a four-month-old plane. Both of those airplanes experienced fault messages and error issues in their planes within the first month of being in service.
And people should be outraged. So when the NTSB says they're going to go in and do a thorough investigation, I have my doubts.
CHAKRABARTI: So you're saying that the NTSB itself in this email to the mother of victims of one of those, the Ethiopian or Lion Air crashes from 2018 and 2019 admits that it did not send anyone to the Boeing factories in Washington State to take a look at manufacturing after these two planes went down.
That's right. They said there was no reason to. They had, they thought that they knew what happened and they had what they thought happened and they thought it was a miscalibrated sensor in the case of the Lion Airplane, and they thought it was a bird strike in the case of the Ethiopian plane.
And that's the stories they stuck with, and they didn't want to hear and look into anything else.
CHAKRABARTI: But that's not what happened. That's not what caused those crashes. As we later found out.
PIERSON: As we later found out, MCAS did activate, it did overwhelm the pilots. The pilots did everything they could to save those planes.
They were not even really aware of this software. But it was not just that was the point. There was other factors that played a role here and that we're never investigated. And now we're seeing, in our opinion, we're seeing evidence of this lack of investigation. Because we're seeing lots of issues with in-service airplanes.
CHAKRABARTI: Let me just ask you quickly here, aviation, as you know better than anyone, is an incredibly complex industry. Just speaking purely from the technological standpoint. As we have seen in other really complex industries, the government knows that it doesn't necessarily have the adequate expertise in-house to put that super fine-tooth comb on every single part of the process.
And so for quite some time there has been a degree of, I don't want to call it self-regulation exclusively. Because that's not what it is. But cooperation between manufacturers, Boeing and the FAA or the NTSB. Where the regulators rely on Boeing to give them good data on the manufacture of their airplanes.
First of all, is that a fair description of how that works?
PIERSON: Yes, it's very complicated and yes, the government relies on the industry quite a bit. But I would just very quickly say that FAA has more than enough resources. They have 45,000 employees, 15,000 are air traffic controllers, so there's 30,000 other employees, but the busiest airplane factory in the world, they were only able to devote four or five people to. And their headquarters, their regional headquarters, is right down the street. It has 1,600 employees. So they have the adequate resources. It's a matter of using the resources more effectively.
CHAKRABARTI: Okay. But so just to be clear, the regional headquarters, regional being the keyword is in Washington state for Boeing, but their corporate headquarters are in Chicago.
PIERSON: Sorry, I didn't mean to confuse you. Boeing's corporate headquarters moved from Chicago to Arlington, Virginia.
CHAKRABARTI: Okay.
PIERSON: Obviously to get closer to lawmakers so they could focus on lobbying. But what I was speaking to was the FAA, whose headquarters is in Washington, D.C. They have a regional headquarters that's very close to the 737 factory that has 1,600 employees in that FAA building. And right down the street at the busiest airplane factory in the world, they've been able to deploy four or five people. And they've increased it to 20, which is woefully inadequate. They just did that within the last couple weeks.
CHAKRABARTI: Okay.
PIERSON: But again, 20 people in a facility that's got thousands of employees working seven days a week, three shifts is a joke.
CHAKRABARTI: Yeah. It reminds me of a time when before Boeing went through that big merger with McDonnell Douglas. Is that right? But McDonnell Douglas, I can't keep all the mergers in track.
PIERSON: Yes.
CHAKRABARTI: But so their headquarters was in the Seattle area. And perhaps at that time, the corporate culture was entirely different too, but you had said earlier, Ed, that you don't think that C-suite folks walk the production line enough, if at all.
And one of the reasons might be because they're really far away versus when leadership was right there, right next to where the planes were being made.
PIERSON: But you have to understand that the board of directors in the C-suite and executives in the Boeing company, there's a whole fleet of aircraft called Boeing Business Jets.
They're actually luxurious jets that all they do is they transport senior executives of the company around all over the globe. And so they're perfectly capable. These board of director members are making over $300,000 a year. And they have a fiduciary responsibility, and the public should absolutely be demanding that they get out. And out where the people that are building these airplanes and these providing these products and services are at, for them to not go out and spend time on the factory floors of the company is inexcusable.
It's negligent. And so all they're doing is sitting back and having people spoon feed them, like CEO Calhoun. I've heard so many. There's a lawsuit that just came out from the Rhode Island, a Rhode Island shareholders group. And in it they quote the Boeing CEO, probably 30 times on promises he's made about renewed focus on quality and safety.
And as far as we're concerned, really nothing changed. He went, the former CEO was removed right after I testified. And Calhoun became the CEO. He had been on the board for 10 years. He's been part of the problem. And the people that I get contacted all the time, because I live in Seattle, Washington area, I get contacted all the time by Boeing employees that are expressing frustration on the pressures that they're under.
And the push to get these planes out the door. Because all the discussion is, if you go back and look, the CEO spends probably 80% of his time talking about how many planes they're going to deliver and meet Wall Street. And he should be out there talking about quality. And I don't care how many planes you can build, I want to know how many planes high quality you can build.
That's what you need to be doing. And so talk is cheap.
CHAKRABARTI: Let me play something here from what happened just last week. This is FAA Chief Michael Whitaker, and he testified before Congress, of course, after Alaska Air 1282's door plug blowout. Dina Titus, democratic Congresswoman from Nevada raised concerns about whether companies, a.k.a. Boeing, were prioritizing profits over safety.
DINA TITUS: We're seeing more and more in different modes of transportation that companies are acting in ways that tend to prioritize profits over safety. And you mentioned in your testimony that the agency found inspections of the grounded 737 MAX 9 aircraft, showed Boeing's quality system issues were, and I quote, unacceptable and required further scrutiny.
Do you have confidence then your suppliers, they can kind of maintain this quality control? It's not a fox guarding the henhouse kind of situation.
MICHAEL WHITAKER: I think we're looking, we're going to look at this process really top to bottom to see where the incentives are, where the failures are in the system. And we're going to demand that quality come up to the appropriate schedule. We certify aircraft to be built to very specific specifications, and they have to be built to those specifications. So regardless of their other motives they're not going to be able to build more airplanes until they meet those standards.
TITUS: Okay. You don't see a problem with conflict of interest with self-inspections.
WHITAKER: We are looking at that specifically. We've asked MITRE, our research firm to give us options on delegation and where we might bring in a third party, for example, in quality control or quality assurance to make sure you have a neutral set of eyes on some of those issues. So that is something we're looking at.
CHAKRABARTI: Okay, so that was FAA Chief Michael Whitaker last week testifying before Congress about who's really guarding the hen house here as Democratic Congresswoman Dina Titus put it. Now we have to take a quick break here, but when we come back, we will go through a little bit of the NTSB's preliminary report that they released just last week about Alaska Air 1282, because I think it reveals some very specific things about the kinds of failures and concerns that Ed Pierson has been talking about that he saw on the line when he worked at Boeing 737 MAX Factory in Renton, Washington.
Part III
CHAKRABARTI: Now, as I mentioned earlier, we did reach out to Boeing to see if they could give us a comment, a statement, provide someone for today's show.
They declined to do that, but they did point us to some of the things that Boeing CEO David Calhoun said in a quarterly earnings call for the fourth quarter of 2023. So here's a little bit of what he told investors.
CALHOUN: We caused the problem, and we understand that. Over these last few weeks, I've had tough conversations with our customers, with our regulators and congressional leaders and more.
We understand why they are angry, and we will work to earn their confidence. There is no message, no slogan, that will accomplish that. It's all about real demonstrated action and absolute transparency. Every step of the way.
CHAKRABARTI: CEO David Calhoun of Boeing in a fourth quarter, 2023 earnings call. And I said that was for investors.
It's for the financial press really. But Ed, okay. I know you probably have comments to what Calhoun says. We'll get to that in a second. But when he says we caused the problem, and we understand that, I'd like to dig into what the NTSB preliminary report finds. Okay. So first of all we keep calling it a door plug, but can you just describe specifically what that is?
It's actually, it is what would've been an emergency exit on a differently oriented craft. Is that right?
PIERSON: Yeah. On airplanes, like Ryanair has that model where they have more people they cram into the plane and they have to have an additional exit. So really it is an exit on other models, and they just plug it up for the purposes of the 737-9 model.
CHAKRABARTI: Okay, got it. So the NTSB really points to four missing bolts, essentially. And they go, that were on, that were supposed to be on this door plug. And they describe how those bolts went missing. So again, just to remind folks, this plane was delivered to Alaska Airlines on October 31st of 2023.
And in the NTSB report, when the plane was being manufactured, they note that on September 1st there was basically an engineering sort of errors report within the manufacturing process that said, "Hey, there were five damaged rivets on one side of the frame of where that door plug was." So they had to fix the rivets.
Obviously, that seems to be standard practice Ed. Can you just briefly tell me what is the normative process when an error like that is found? What's supposed to happen to document that it was appropriately fixed?
PIERSON: First of all, you have to understand that fuselage comes in from spirit AeroSystems in Wichita, Kansas.
It gets trained into the factory. When it gets loaded into that first flow day or even before that, they're supposed to inspect that fuselage and then during the course of that inspection, in the past we have seen defects that have been delivered to the factory. Employees are on the lookout, and they apparently noticed the five rivets that were damaged, and they decided they needed to repair it, which is the right thing to do then. But this is all supposed to be documented. There's systems where you document the removals of parts and pieces of an airplane. There's quality reports that have to be submitted. There's a lot of processes that are documenting or supposed to document what happened.
CHAKRABARTI: And in fact, they do, right?
They document that.
PIERSON: No.
CHAKRABARTI: They don't? Let me just go through what the NTSB says and you tell me what you think they got wrong. Okay?
PIERSON: Sure.
CHAKRABARTI: Because they have this photograph, and it shows the places where the rivets were missing or needed to be replaced. And so according to the NTSB, in order to do that, they had to open that door plug.
That's the real culprit here. And in order to open that, they had to remove bolts. So they do that. And then later on in the report, when they replaced the door plug, there's a photograph, which again, I presumed was just appropriate documentation. But there's actually a photograph showing that four of those bolts weren't replaced into the door plug.
So what went wrong there? Or what could have gone wrong since you weren't there at the time?
PIERSON: Well, a lot of things could have gone wrong, but when you asked me, was the paperwork filled out and did they follow the processes? There's one sentence in that NTSB report that should be highlighted in yellow and red actually, and I'm going to read it to you. It's on page 17.
It says, "The investigation continues to determine what manufacturing documents were used to authorize the opening and closing of the left mid exit door during the rework." Now this is a month, over a month after the accident, and the NTSB doesn't have, hasn't determined what the paperwork, the records, and these records are supposed to be. They're immediately available. They're electronic, so they should have, the NTSB should have known this within an hour of them opening their investigation. Those records should have been made immediately available to them, and it will either show that the paperwork was done.
Or it was done incorrectly or not done at all. And this is really important, because people are fixated on the four bolts. There's an accident causation investigation technique. One of the techniques is called five whys, and it's really pretty straightforward. People do it intuitively. Why did the door blow off the plane? Because there were four bolts missing. Why did the, why were the four bolts missing? Because employees forgot. Why did they forget? They failed to fill out the paperwork. Why did that happen? They were tired and it was in between shifts. Why did that happen?
They were rushing to get the planes out the door. And eventually when you pull that string and you keep following it, the root causes appear. And the root causes are not just a single employee forgetting to put four bolts in, but a production system that is dangerously unstable.
CHAKRABARTI: Is there supposed to be a process here?
I'll get back to your point about NTSB saying they still haven't found the right documents, but is there supposed to be a process here when any portion of an aircraft that's being built gets removed in order to fix something else that, is there another engineer who comes by and just checks that everything has been replaced appropriately?
PIERSON: Yes, there are all kinds of processes that are supposed to record the issue. Like my employees that worked on the factory floor, when the mechanic or a technician came over to them and said, "Hey, I'm missing a part, or it's damaged, or I'm missing an engineering drawing." Then there's a documentation of that.
It goes into a database; people are alerted and then people that are supposed to fix the problem or come down to the factory floor and assist the employees. And there's all kinds of documentation. This is what is really concerning. Because this is, I hate to say it, but it harkens back to the two fatal crashes.
Because the NTSB did not go into the factory, did not look at those production records. Had they looked at those production records, they would've seen the two planes that crashed, had electrical issues on those planes. So this whole thing, everybody is fixated on the bolts, but they have to understand, like you said, Meghna.
This is a complicated process and it's much more complicated, and they just patched it up and said it's good and everything is fine, and it's not.
CHAKRABARTI: Yeah. I was fixated on the bolts as the end point of a series of failures that had to proceed it, right? Correct. In order for a highly sophisticated manufacturing facility to do something as just egregious, let's just put it that way, as not replace bolts on a door panel. There's failures that had to come before that. And so that's why, you're noting about was it properly documented? Why doesn't the NTSB have that documentation yet? These are all the things that not only you and I here today, but hopefully Boeing and federal regulators are really wrestling with now.
But Ed, you've said a couple of times here that you're really troubled by what you called as planes being rushed out the door before you left in 2018. Now, Boeing claims they don't do that anymore. In that same Q-4 earnings call, so it was a recent, very recent earnings call, had to be after the Alaska Airlines disaster here, or the debacle. Once again, here is Boeing CEO David Calhoun, and here's what he said.
This increased scrutiny, whether it comes from us, from our regulator or from third parties will make us better. It's that simple. Over the last several years, we've taken close care not to push the system too fast, and we have never hesitated to slow down, to halt production or to stop deliveries to take the time we need to get things right.
Nobody knows that better than our investors. As we stopped delivering 787's for over a year to ensure that each conformed to our exacting specifications prior to delivery.
CHAKRABARTI: Boeing CEO David Calhoun, and I want to re-emphasize that we did reach out to Boeing for specific statements regarding questions we would've asked today, but they pointed us to this earnings call, which took place on January 31st.
Ed, he says right there, we don't push the system.
PIERSON: That's not true. In fact, I hate to say it, but it's actually untruthful, completely not true. They pressured the system. The company has only shut the factory down twice in recent years. Once it happened right after Congress said that they were going to do a much more investigation and right after the crashes. And then they shut it again right after that because of the pandemic. So what the CEO is saying is completely incorrect. And what you have to also understand as evidence that I'm so tired of hearing these broken promises, this airplane has had over 20 serious production quality defects. And so when he says that we don't deliver safe planes, just yesterday --
CHAKRABARTI: Or don't deliver unsafe planes, but go ahead.
PIERSON: Yeah, that's right. Just yesterday, another message came out from the FAA saying they had electrical defect in the standby power control unit, which is a very important component in the flight station, which controls part of the pilot's displays and instrumentation that came out yesterday. In the last month, they've reported on rudders that have had missing nuts.
They've had hundreds of mist-drilled holes. They've had fuselage defects of improper shimming. I could go on and on. Electrical bonding and grounding defects. Loose pilot rudder, pedal cover fasteners. The truth of the matter is he's expecting, they're expecting people to go to sleep and not pay attention, but we are paying attention.
And there's been incidents just in the last month and a half, there's been two airplanes that had to do emergency descents because of engine to icing not working. There's been a compressor stall. They've had stab trim motor failures. I don't know what information he's looking at, but I would love to have an opportunity to sit down and show them the information we're looking at because they're asleep at the wheel.
CHAKRABARTI: Ed, it sounds like you're saying that there needs to be a re-grounding of the 737 MAX. And you just described errors or anomalies that go from nose to tail.
PIERSON: Yes. And not only, we actually, our foundation, last week, we actually feel so strongly about it. We don't want to mince words. Because we don't want to keep risking people's safety.
We recommended it grounded. And another thing you have to understand also is there were thousands, I got to stop and just pause. Because it gets me upset. There were thousands of quality control inspections that have been removed on these airplanes. And I'm talking individual airplanes.
Not all the airplanes, but there was a program that started in about 2017 to remove inspections. Because it could accelerate production and the executives all know about it. Because they were the ones who sponsored it. And the planes that crashed had inspections removed from them. There's been other, this program expanded out.
It was called QA Transformation Plan. Then it became what's called Verification Optimization. They removed thousands of quality control inspections, not just on the 737 MAX airplanes, but on other airplanes, 77 7, 787. And this was done, and what we realize and what we found out is this was done without the FAA's knowledge in most cases.
Wrap your head around that. The company had two fatal crashes, killed 346 people, over a $20 billion loss to the company. Criminal charges being placed for criminal fraud still in the courts, and the company is removing quality control inspections. Quality control inspections have been in place for decades, which contributed to the success of the quality of that airplane.
It's criminal.
CHAKRABARTI: As I say, once again, we did contact Boeing. We did and they pointed to us, to those earning calls. You said those inspections had been in place for decades. I do want to just take one quick second to listen back to someone we talked to in 2020 after the Ethiopian and Lion Air crashes.
Her name's Cynthia Cole, and she's a former test and systems engineer at Boeing. She worked there for 32 years. Retired in 2010 and she told us about how the company used to operate and the high standards and cultures of the Boeing of old.
CYNTHIA COLE: If there had ever been any incident on any of those aircraft, we would've known every single part by serial number and part number of any piece on that aircraft. We had such meticulous records. During those days, at the Boeing company, we had to document, if you couldn't document your process step by step, you didn't have a process.
And that was one of the things that made the Boeing company excellent, was the systems engineering. And so we always thought, schedule and cost, any profits. And staying on track. That would follow if you did the job right. The most important thing was doing the job right. And then the profits would come, and everybody had that mindset.
CHAKRABARTI: Former Boeing engineer Cynthia Cole took to us in 2020. Ed I only have about a minute-ish left here with you. Yeah. So we got to wrap up, unfortunately. But my last question to you is specifically what do you, what would, what's going to take to fix this problem at Boeing? What would you have Boeing do right now, and what would you have federal regulators or even Congress do right now?
PIERSON: We're probably going to need another podcast to do that or another radio show, but I will tell you we're meeting with head of the FAA. Members of our foundation are meeting with the head of the FAA and the Deputy Secretary of Transportation on March 8th, and we're going to give our specific recommendations.
I will tell you that a woman that just talked is 100% correct. She's absolutely, nobody could have said it better what she said. I 100% agree with her. The other thing I want to point out that people need to know is there's legislation right now at the Senate, it's the FAA Reauthorization Act, and there was nine recommendations that victim family members put together.
These individuals who have been fighting tirelessly for years, ever since they lost loved ones, have been trying to get Congress to make recommendations, very specific, very well thought out, recommendations, and basically none of them are being included in the FAA Reauthorization Act. And right now, that's on Senator Cantwell's Committee and Senator Cruz.
So I encourage people to contact their legislators and make sure those recommendations are included.
This program aired on February 15, 2024.